by The Embroidery Coach | | Organizing
In Part 1 of Organizing Your Embroidery Business, I talked about organizing your information that you use in running your embroidery business. In Part 2 I l talked about your customers design information. In Part 3 I am going to talk about your Production process.
The first step of my production process is to log in the job on the log in form, make a list of new artwork that has to be created and either gives that to the person that creates the artwork or sends it out to the digitizer. If I have to order anything for the project, I do so and put a copy of the original customer order in a plastic sleeve and hang it in the receiving area waiting for the goods to come in. A production form is filled out with the customer and job information on it that follows through the entire production process. The original order is placed into the customers file folder in the office. I connect that order and the production form with the goods when they arrive.
After the design is ready, I place that with the order and it is then placed onto a shelf ready for hooping. If you have employees, it is best to have at least one job hooped ahead of time. This creates a smoother and faster production flow. When I had my large embroidery business, I have all of the jobs hooped the day before they were placed onto the embroidery machines. I had 24 dozen hoops of the most popular sizes (12 centimeter and 15 centimeter) so that this was possible, unless the order sizes were larger than 24 dozen. Sometimes this was the case, but at least the first 24 dozen pieces for the job was hooped ahead of time.
At the time for embroidery, the baskets of hooped garments are moved to the embroidery machine area and the machine operator can start the embroidery process. The design is loaded into the machine by whatever process you use to get your designs into the machine. The garment are then loaded onto the machine and embroidered. After they are embroidered, they are removed from the machine, unhooped and placed into another basket or bin and moved to the trimming area.
The trimmer will trim, steam, fold and pack the garments ready to be shipped. In a large business this will be more than one person. You will have a person that trims and steams and another one that will fold and pack the garments ready for shipping.
The production form is filled out by the operator with all of the information about each process as it passes through production.
Part 4 of Organizing Your Embroidery Business will be about shipping and invoicing procedures.
by The Embroidery Coach | | Embroidery Business Planning
A business plan will give you a clear direction on the steps you intend to take in the running of your embroidery business and help you to stay on track so that your business can grow.
A key element to writing a great, actionable embroidery business plan is to take it piece by piece. You can begin by planning out your day-to-day actions. A great Simple Working Plan needs to be laid out at the end of every day. Set aside a few minutes to write down the things that need to be done the following day, prioritize them, and you are ready for the next day‚’s work.
When you are in the habit of planning the next day‚’s work, you can move on to planning your week. At the end of every week, set aside some time to lay out your next week‚’s work. This will help you to know if you have spots open for more embroidery work as it comes in.
As the planning progresses and you are able to schedule out a few weeks' worths of work, you are then ready to really think about how to plan out your entire embroidery business.
An important part of any business plan is to include how you intend to check your progress along the way. Because there are so many different types of business plans, some you find may already include this, and some may not. In either circumstance, you will want to create for yourself a simple plan or roadmap to help you check your progress and make sure you are staying on track.
This simple embroidery business plan will require you to do some research on your embroidery competition, what is going on in your market and what you can do to stand out from the crowd.
You will also want to write down why you want this embroidery business and what goals you intend to reach as a result. These will be your markers and help you to create a plan that is real and one that you will actually use!
Now, if you are planning on seeking financial assistance, then you will need to progress to a formal business plan. This will take some more research so that you have the right facts and figures to present to the financial institution. Take your time and fill this in as you use your simple business plan.
It does not matter if you are using a simple plan only or if you are writing a formal Embroidery business plan, it is important to remember that you will be making changes to your embroidery business plan and will adjust it as you go, just make sure that you are referring to your plan to help keep you on course and using it to help you make the right decisions.
Joyce Jagger
The Embroidery Coach
by The Embroidery Coach | | Embroidery Business Marketing
I want to share with you how to create a system for embroidering team names on jackets or shirts. This time-saving system that I came up with for embroidering team names on jackets or shirts is very simple and as indicated, it is a huge time saver! I take my list of names that I received from my customer and arrange my items in the same order as the names on the sheet.
I take the list of names and put it on my copier and increase them in size by 200%. After that, I will cut all the names apart on my sheet and then tape them to each item according to the size.
After that, I hoop all the items and then stack them in order according to how they’ll be embroidered and how the names are on my sheet because I don’t want any mistakes. That is in the exact same order that the customer gave them to me and that’s how I will be sending them back.
When I set up the names in my Pulse software, I set them up in a Name Stack. By that I mean I set up each name, put a color change between each one and then literally stack one name on top of another name in the software. This way they all start in the center and in the exact same place.
With the color change command between each name, I set the machine so that it automatically stops when it sees a color change command. When I put the first item into the machine and get it all set in place for the first name, it will embroider the first name and then stop.
This allows me the time to take out that first item and put in the next item on the list. I continue this until I am finished with the entire list of names. As the next one is embroidering, I remove the hoop, trim and stack the last one. I can embroider about 40 items in an hour on a single head machine using this method.
If you have a multi-head machine, you load the entire machine, again in the right order that the names will be embroidered, turn all of the heads off except head no. 1. Start the process with head no. 1 and when the first name is completed, turn off head no. 1 and turn on head no. 2 and continue this process until each one is completed.
You can create this system for embroidering names on jackets in any embroidery design software. It will work, trust me on that! No matter what I am charging, wholesale or retail this is a huge moneymaker! Try it, you will like it, I promise.
You can see how to go through the embroidery process inside of the Embroidery Business Academy in Skill Set No. 1. You will find it in Embroidery Production, inside of Embroidery Basics.
If you are interested in receiving this tip and a new one each day, Click Here!
by The Embroidery Coach | | Embroidery Business Marketing
In today’s world of rising prices and uncertainly, we need to be prepared to not only help our customers, but also make sure we can pay our bills! We are running a business, not a charity organization!
I was very excited about our new year and hoping that we could finally get back to normal and then we get hit with all of our supplies and the cost of freight going through the roof. What does that mean to us as far as our business is concerned?
It means that we have to raise our prices. You cannot absorb all of these costs. You must go into your pricing structure and make your adjustments for all of these price increases.
Ask yourself these questions:
- Am I paying more for the freight of my supplies?
- Am I paying more for the thread, bobbins, backings or stabilizers?
- Am I paying more for labor?
- Am I paying more for payroll taxes?
- Am I paying more for the products that I am ordering for my customers?
I have noticed a huge increase in every one of these. I am getting emails from my embroiderers complaining about all of this and what should they do? They keep telling me, “We are having a hard enough time trying to get people to pay our prices as it is, now we have to raise them? How can we do that and get in the job?” How can we stay in business?
Many embroiderers have gone out of business since the pandemic started, but many embroiderers have started businesses. The large companies that I work with have successfully raised their prices and are extremely busy. You have to do this too!
Embroiderers; everyone knows that you have to raise your prices. The price increases have hit every person on the planet, not just the embroiderers. Your customers understand that they are going to have to pay more for your services if they want to be able to promote their businesses!
Raise your prices! If you are having a tough time doing that or need some help with it, contact me. I have an excellent program that will help you get your Pricing structure together, one that will help you make money! Don’t put this off, get it done today before you end up having to close your doors!
by The Embroidery Coach | | Embroidery Business Marketing, Embroidery Education
Setting up the lettering to Embroider on the back of a mesh cap can be done very easily if it is done correctly. There is more than one way to accomplish this, but the way that you select will depend on the actual design that you plan on selecting or creating. Many embroiderers are afraid to try this, but if you follow the simple directions, I will try to make it easy.
If it is a text-only design, the small letters can get lost in the mesh and you will need to add a knockdown stitch under the lettering.
If it is a design that is a heavy complex fill design and no small lettering is outside of the area of the design, you can simply add a piece of topping to cover the entire area before you begin the actual sewing operation.
The Areas That I Will Cover In This Article
- The different ways you can create the lettering
- I am going to show you how to set up the lettering
- The process of creating the lettering
- Explain how to create the knockdown stitch
- Explain the settings I used and why I used them
I am going to show you how I set up the lettering to embroider on the mesh cap back using small text lettering only. The lettering that I will be using will be 6 mm or about 1/4 inch in height. I try to keep it to a simple block font that does not have serifs if at all possible. I also want to keep it in uppercase only, as this makes it much easier to read.
At that small size, a font with serifs does not work well because of the size of the serifs.
Different Ways To Create The Text Lettering
I have found that there are about 4 different ways that you could lay down the text lettering for the cap back.
- Horizontal for a straight bottom fitted cap
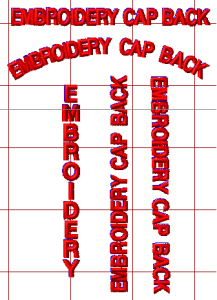
- Arched for a Snap-back keyhole cap back
- Vertical with the lettering starting at the top
- Vertical with the lettering reading up or reading down.
The Basics of Setting Up The Lettering
I used Pulse Embroidery Software to set up the lettering. I started with the basic Horizontal for the straight bottom fitted cap. The font that I used was Block New at 6mm.
Step 1 – I selected my font, set it to 6mm, and then I drew a straight
line across the front of my workspace and typed in the lettering, EMBROIDERY CAP BACK. I then clicked OK and my lettering was on the workspace.
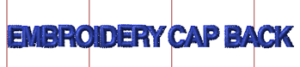
Step 2 – I added Center run Underlay Stitching at 1.5 mm in stitch length because the letters are so small and .20mm for the Pull Compensation settings.
Step 3 – I adjusted my spacing between the letters. You want to make sure that you have all of your settings in place and the lettering exactly as you want it before you add the knockdown fill on the design.
Step 4 – Zoom in on your lettering, turn off the 3D or TrueView of your lettering so that you see the stitch points on your letters.

You will notice that there is very little space between each letter. You want your stitch points to almost touch. This will give you a clean easy run on the machine without the machine adding locks and trims between each letter. You do not want your machine to stop and start between each letter, but you also do not want a thread showing between your letters when it is finished sewing,
Step 5 – Create the Knockdown stitch. Pick up your Complex Fill tool in your digitizing tools and start plotting around the outside of the stitch points of your letters. You do not have to be perfect when you are doing this. You want it to be out and around the letters, but do not draw an oblong around the lettering, because it will show much more. You only want to draw around the shape of the letters.

This is what you will see when you have it completed. You would repeat the same process for the remaining 2 words before you go any further.
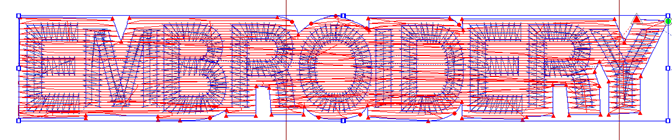
Step 6 – Now you must change the angle of the fill stitches so that your letters do not sink into the fill stitches and reduce the density to about -35 stitches per inch from your normal fill setting. I also added a .30mm pull comp setting to the fill. The image below will show your finished results.

Step 7 – In your Sequence View, move your fill background (knockdown stitch) up before the lettering so that it will sew out before the lettering sews. You will sew the fill stitching the same color as the mesh on the cap. When it is sewn out, you will hardly see the background stitching at all.
Here is a finished Embroidery on the back of a mesh cap. This is a vertical design up the seam of the back of the mesh cap. The fill stitching or knockdown stitch is sewn in white. You cannot see the fill stitching under the letters and the letters sew out crisp and clean.
This same lettering could have been sewn straight across the back at the
Setting up the lettering to embroider on the back of a mesh cap is not hard, it just takes a few minutes and the finished result is amazing.
Click on the PDF to print out How To Set Up The Lettering To Embroider On The Back of a Mesh Cap You will be able to see the images much better.